Revolutionizing Clean Room Doors Manufacturers: Innovations in Clean Room Door Technology for Enhanced Efficiency
Introduction
These controlled environments require stringent measures to maintain cleanliness, prevent contamination, and ensure product quality. Among the crucial components of clean rooms, doors play a significant role in maintaining the integrity of these controlled spaces. As technology evolves, clean room door manufacturers are continuously innovating to meet the ever-growing demands for efficiency, reliability, and safety.
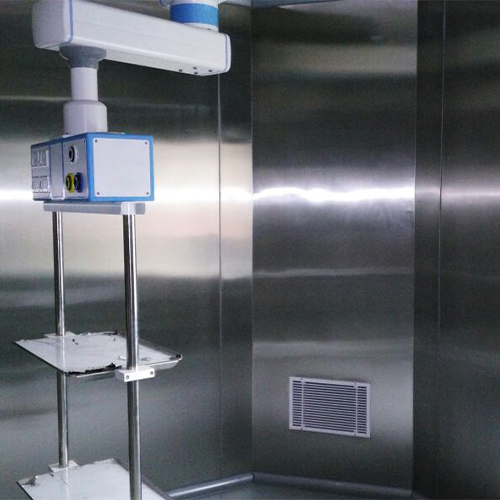
The Role of Clean Room Doors Manufacturers
Clean room doors are not just conventional entrances; they are sophisticated barriers designed to maintain specific environmental conditions within clean room facilities. As pioneers in clean room door technology, Clean Room Doors Manufacturers like Isoflex understand the intricate requirements of these environments. By leveraging advanced engineering and innovative materials, they strive to develop doors that not only meet regulatory standards but also enhance operational efficiency for their clients.
Evolution of Clean Room Door Technology
Clean room doors have come a long way from traditional designs to advanced, technologically sophisticated solutions. Earlier, doors primarily focused on sealing the room and preventing contaminants from entering. However, modern, clean room door technology goes beyond mere sealing. It addresses various challenges, such as air leakage, particle emissions, pressure differentials, and ease of operation.
Innovations Driving Efficiency
Clean Room Doors Manufacturers are continually pushing the boundaries of innovation to develop doors that enhance the efficiency of clean room operations. Some notable advancements include:
- Sealing Technology: Effective sealing is paramount in clean room environments to prevent the ingress of contaminants. Advanced sealing mechanisms, such as pneumatic seals and magnetic seals, provide superior air-tightness, minimizing air leakage and maintaining pressure differentials within the facility.
- Material Selection: The choice of materials plays a crucial role in the performance of clean room doors. Manufacturers are utilizing high-quality materials such as stainless steel, aluminium, and composite materials to ensure durability, corrosion resistance, and cleanliness compliance.
- Automation and Integration: Automation has revolutionized clean room door operations, offering seamless integration with facility management systems. Automated clean room doors equipped with sensors, actuators, and programmable logic controllers (PLCs) enable precise control of access, airflow, and environmental parameters.
- Energy Efficiency: Energy consumption is a significant concern in clean room facilities. Manufacturers are incorporating energy-efficient features such as insulated panels, low-power actuators, and LED lighting to minimize energy consumption without compromising performance.
- Cleanliness and Sterility: Maintaining cleanliness and sterility is non-negotiable in clean room environments. Advanced surface coatings and finishes ensure easy cleaning, resistance to microbial growth, and compliance with regulatory standards such as ISO cleanliness classifications.
- Safety Features: Safety is paramount in cleanroom operations. Manufacturers are integrating safety features such as emergency release mechanisms, anti-trap sensors, and redundant control systems to ensure the well-being of personnel and prevent accidents.
- Dynamic Pressure Control: Isoflex’s clean room doors feature dynamic pressure control systems that automatically adjust door operation based on real-time pressure differentials within the clean room facility. This ensures optimal airflow management, minimizes cross-contamination risks and maintains uniform environmental conditions throughout the facility.
- Anti-Static Properties: Isoflex integrates anti-static properties into their clean room door materials to mitigate electrostatic discharge (ESD) risks. By preventing static buildup, these doors safeguard sensitive electronic equipment and components, ensuring uninterrupted operation and product integrity.
- Noise Reduction Technology: Isoflex’s clean room doors incorporate advanced noise reduction technology to minimize operational noise levels. This not only improves the working environment for personnel but also reduces disturbances to sensitive processes and equipment within the clean room facility.
- Adaptive Seal Technology: Isoflex’s clean room doors feature adaptive seal technology that dynamically adjusts sealing pressure based on environmental conditions. This ensures consistent and reliable sealing performance under varying temperature, humidity, and pressure conditions, enhancing overall operational efficiency and reliability.
- Remote Monitoring and Control: Isoflex offers remote monitoring and control capabilities for their clean room doors, allowing facility managers to monitor door status, access logs, and performance metrics remotely via secure web-based interfaces or mobile applications. This enables proactive maintenance, troubleshooting, and optimization of door operations, irrespective of geographical location.
- Green Technologies: Isoflex incorporates sustainable and eco-friendly materials and technologies into their clean room doors, reducing environmental impact and promoting sustainability initiatives. This includes the use of recycled materials, energy-efficient components, and eco-friendly manufacturing processes, aligning with global efforts towards environmental conservation and corporate responsibility.
- Customization Options: Isoflex provides extensive customization options for its clean room doors, allowing clients to tailor door designs, sizes, finishes, and functionalities to meet specific application requirements. Whether it’s specialized sealing requirements, unique access control features, or aesthetic preferences, Isoflex works closely with clients to deliver bespoke solutions that perfectly align with their needs and preferences.
- Augmented Reality (AR) Maintenance Assistance: Isoflex employs augmented reality (AR) technology to provide interactive maintenance assistance for their clean room doors. Maintenance technicians can access AR-based instructional guides, troubleshooting procedures, and interactive simulations directly through smart glasses or mobile devices, streamlining maintenance processes and reducing downtime.
- Predictive Maintenance Algorithms: Isoflex utilizes predictive maintenance algorithms and machine learning techniques to analyze data from sensors embedded within their clean room doors. These algorithms can predict potential equipment failures, identify emerging issues, and recommend proactive maintenance actions, ensuring optimal performance, reliability, and uptime of clean room door systems.
Isoflex: Leading the Way in Clean Room Doors Manufacturers
As a renowned Clean Room Doors Manufacturer, Isoflex has been at the forefront of clean room door technology for decades. With a commitment to excellence and continuous improvement, Isoflex has introduced several groundbreaking innovations in clean room door design:
- Modular Design: Isoflex’s modular clean room doors offer unparalleled flexibility, allowing for easy customization to fit varying clean room configurations. The modular design also facilitates quick installation and minimal disruption to ongoing operations.
- Integrated Access Control: Isoflex’s clean room doors are equipped with state-of-the-art access control systems, including biometric scanners, RFID readers, and keypad entry systems. These systems ensure authorized personnel access while maintaining security and traceability.
- Smart Monitoring and Analytics: Isoflex’s clean room doors are IoT-enabled, allowing real-time monitoring of door status, environmental parameters, and performance metrics. Advanced analytics provide valuable insights for predictive maintenance, optimizing door operation, and compliance tracking.
- Zero-Gravity Operation: Isoflex’s innovative zero-gravity door technology revolutionizes clean room door operation. By employing counterbalanced mechanisms and precision engineering, these doors offer effortless, smooth operation while minimizing wear and tear on components.
- Seamless Integration: Isoflex’s clean room doors seamlessly integrate with existing clean room infrastructure and automation systems, ensuring compatibility and interoperability. Whether it’s a retrofit or a new installation, Isoflex’s doors can be easily integrated without disrupting workflow.
Conclusion
Innovations in clean room door technology are essential for meeting the evolving needs of modern, clean room facilities. Clean Room Doors Manufacturers like Isoflex are leading the way with advanced solutions that enhance efficiency, reliability, and safety. By embracing cutting-edge technologies and continuous improvement, these manufacturers are empowering industries to maintain the highest standards of cleanliness, productivity, and product quality in their clean room operations. As the demand for cleanroom solutions continues to grow, the future promises even more exciting advancements in cleanroom door technology, driving further improvements in efficiency and performance.