Revolutionizing Building Insulation: Innovations in Rockwool Sandwich Panels Manufacturers
Introduction
In the ever-evolving world of construction and architecture, there is a constant quest for materials and technologies that offer superior performance, energy efficiency, and sustainability. One of the key players in this pursuit is Rockwool, a renowned name in the industry known for its innovative solutions in building insulation. This blog post delves into the latest innovations in rock wool sandwich panels and doors, showcasing how Rockwool Sandwich Panels Manufacturers and Rockwool Doors Manufacturers are changing the game.
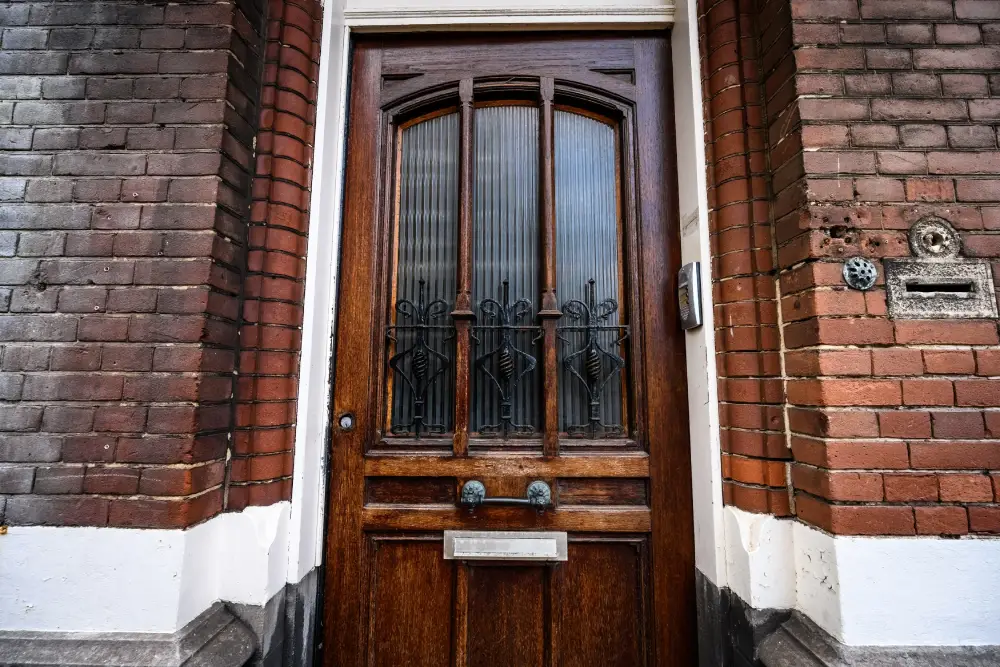
Rockwool Sandwich Panels: A Brief Overview
Rockwool sandwich panels, also known as mineral wool sandwich panels, are a versatile building material that combines the exceptional insulating properties of rock wool with the structural strength of metal or other facing materials. These panels are widely used for roofs, walls, and partitions in the construction industry. They offer several advantages over traditional construction materials, including enhanced thermal performance, fire resistance, and sound insulation.
UInnovation #1: Improved Thermal Performance
One of the primary concerns in modern construction is energy efficiency. Buildings are responsible for a significant portion of the world’s energy consumption, and it is imperative to reduce this impact. Rockwool sandwich panels have long been recognized for their exceptional thermal insulation properties, but recent innovations have made them even more efficient.
New manufacturing techniques and materials have allowed Rockwool Sandwich panel manufacturers to create panels with lower thermal conductivity. These panels offer better insulation, reducing heating and cooling costs for buildings. The improved thermal performance helps meet the stringent energy efficiency standards in many countries, making rock wool sandwich panels an ideal choice for architects and builders aiming for green and sustainable construction.
Innovation #2: Increased Fire Resistance
Traditional building materials like wood and some insulation products can pose a significant fire risk. Rockwool sandwich panels, however, are inherently fire-resistant due to the nature of rock wool itself.
Rock wool door manufacturers have recently developed advanced fire-resistant doors using rock wool as the core material. These doors are designed to withstand extreme heat and fire, providing valuable time for occupants to evacuate a building in case of a fire. The combination of fire-resistant properties and high thermal insulation makes Rockwool doors essential in creating safer and more energy-efficient buildings.
Innovation #3: Enhanced Acoustic Insulation
Acoustic comfort is often an overlooked aspect of building design. However, it is crucial in creating spaces conducive to work, relaxation, and overall well-being. Rockwool sandwich panels have always been appreciated for their sound insulation properties, but continuous innovation has taken this to the next level.
Rockwool Sandwich panel manufacturers have developed panels with improved acoustic insulation properties. These panels are used in commercial and industrial buildings and residential constructions to create quieter, more peaceful living environments. The enhanced sound insulation provided by rock wool sandwich panels is a testament to their adaptability in various construction applications.
Isoflex, Rockwool Doors Manufacturers: A Game-Changer in Building Safety
Rockwool doors are another critical innovation in the world of construction. They offer unique properties that make them indispensable for residential and commercial buildings.
Innovation #1: Unrivaled Fire Resistance
Fire resistance is a recurring theme in the innovations brought about by Rockwool Doors Manufacturers. Rockwool doors are engineered to withstand high temperatures and flames, providing a critical layer of protection in a fire. Their ability to maintain structural integrity even under extreme conditions is a testament to the outstanding fire-resistant properties of rock wool.
Innovation #2: Energy Efficiency
In addition to their fire resistance, Rockwool doors also contribute to energy efficiency. By providing excellent thermal insulation, these doors help maintain a stable indoor temperature. This leads to reduced energy consumption for heating and cooling, resulting in cost savings for building owners and a decreased carbon footprint.
Innovation #3: Enhanced Security and Durability
Rockwool doors are known for their durability and robust construction. They are resistant to wear and tear, making them a wise investment for any building. Their security features are also top-notch, providing peace of mind to property owners.
The Sustainable Advantage
In the construction industry, sustainability is no longer an option; it’s a necessity. Rockwool sandwich panels and doors align perfectly with this ethos.
Sustainable Innovation #1: Recycled Materials
Rockwool Sandwich Panels Manufacturers have been increasingly using recycled materials in their products. This reduces the environmental impact and minimizes the use of new resources. It’s a win-win situation for both the construction industry and the planet.
Sustainable Innovation #2: Longevity and Durability
The long lifespan of rockwool products, combined with their low maintenance requirements, makes them inherently sustainable. Building materials that stand the test of time reduces waste and the need for replacements.
Sustainable Innovation #3: Energy Efficiency
The energy efficiency offered by rock wool sandwich panels and doors reduces energy consumption, resulting in lower greenhouse gas emissions. As the construction industry strives for sustainable solutions, these innovations are instrumental in achieving sustainability goals.
Meeting the Needs of the Modern World
In a world increasingly conscious of its environmental impact, the innovations in rock wool sandwich panels and doors are more than just technological advancements. They are responses to the ever-evolving demands of modern construction.
Meeting Demands #1: Building Regulations
Stringent building codes and regulations require materials that meet high safety standards, energy efficiency, and environmental responsibility. Rockwool sandwich panels and doors meet these requirements and often exceed them.
Meeting Demands #2: Sustainable Building Practices
The shift towards sustainable building practices has created a demand for eco-friendly, long-lasting, and energy-efficient materials. The innovations in rock wool products align perfectly with these goals.
Meeting Demands #3: Comfort and Quality
In addition to safety and sustainability, occupants of buildings expect a high level of comfort and quality. Rockwool sandwich panels and doors provide acoustic and thermal comfort, enhancing the quality of life for building occupants.
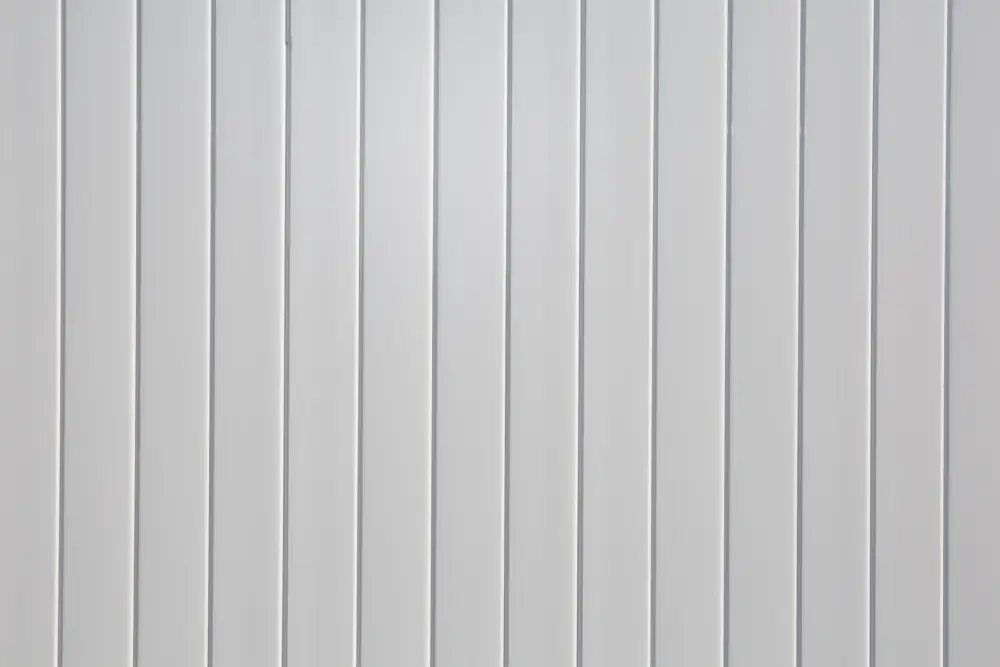
Conclusion: The Future of Construction
In the fast-paced world of construction and architecture, innovations in building materials play a pivotal role in shaping the future. Rockwool sandwich panels and doors, with their improved thermal performance, fire resistance, and acoustic insulation, are at the forefront of this evolution.
Rockwool Sandwich Panels Manufacturers and Rockwool Doors Manufacturers are meeting industry demands and setting new standards for quality, safety, and sustainability. As construction practices evolve, these innovative products will undoubtedly remain at the heart of the building industry, offering a foundation for safer, more energy-efficient, and environmentally responsible structures.
So, if you’re searching for superior building materials that meet and exceed modern construction standards, look no further than rock wool sandwich panels and doors. These innovations are not just a choice; they are the future of construction.